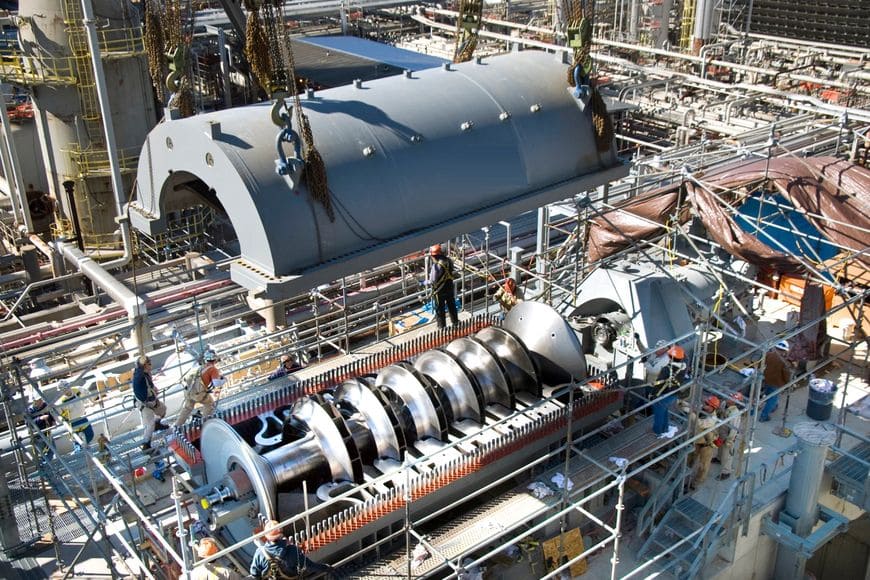
Использование предиктивной аналитики в обслуживании насосного оборудования на НПЗ
А. РЫБАКОВ – руководитель IT продукта по предиктивной аналитике в промышленности, Ctrl2GO Solutions (входит в ГК Ctrl2GO)
На любом нефтеперерабатывающем предприятии основным видом оборудования, независимо от технологической специфики, является насосно-компрессорное оборудование (НКО). Оно обеспечивает все физические и химические процессы, протекающие на любой установке: ректификацию, теплообмен, гидроочистку, риформинг, изомеризацию, каталитический крекинг и т. д. Каждый крупный НПЗ располагает парком насосно-компрессорного оборудования от 1500 до 3000 единиц.
Сегодня средний возраст российского нефтеперерабатывающего завода – свыше 60 лет, большинство крупных НПЗ с объемом переработки более 1 млн тонн в год эксплуатируются уже дольше полувека (данные Минэнерго России). Масштабная модернизация, которая проводилась в отрасли в 2019-2020 годах, не привела к полной замене НКО: до 20-30% насосов на производстве могут быть старше 30 лет и большинство отказов происходит как раз по причине их неудовлетворительного технического состояния. Более современное оборудование иностранного производства тоже требует пристального внимания: после ухода западных вендоров с рынка могут возникать сложности с его обслуживанием.
Затраты на эксплуатацию насосов
Затраты на эксплуатацию насосно-компрессорного оборудования складываются из двух частей. Первая – издержки на обеспечение работы, техническое обслуживание и ремонт. Вторая – потери из-за отказов оборудования и упущенной выгоды.
Производственный процесс на нефтеперерабатывающем или нефтехимическом заводе должен быть непрерывным и идти 24 часа в сутки. Эту непрерывность обеспечивают именно насосы и компрессоры, поэтому все позиции резервируются. Обычно это 100% резервирование: если конкретная единица НКО отвечает за подачу сырья, то для этой технологической позиции на заводе будет два насоса, один из которых находится в эксплуатации, а второй остается в резерве и включается в случае остановки или отказа первого.
В подавляющем большинстве случаев, при отказе или выходе из строя, НКО ремонтируют, и такой ремонт занимает от одних суток до 4-5 дней.
Случается (и такие случаи нередки), что отказывает один насос, а затем, до окончания его ремонта, выходит из строя и второй. Поскольку все технологические установки взаимосвязаны, выход из строя одного из элементов нарушает работу всего предприятия. Более того, поломка конкретной единицы НКО может стать причиной повреждения другого оборудования.
Такое повреждение или выход насосов из строя чревато существенным материальным ущербом для предприятия и даже создает риск травм и гибели сотрудников. Производительность среднестатистического российского завода составляет 12 млн тонн в год. Сутки простоя только одной технологической установки (например, ректификационной колонны) из-за сбоя в работе основных и вспомогательных насосов могут обернуться миллионными убытками. При отказе насоса, в зависимости от критичности его расположения, недополученная прибыль может достигать сотен миллионов рублей в день.
Важно также учитывать энергоэффективность насосов: насосно-компрессорное оборудование является основным элементом любой установки и на его долю приходится 70-90% потребляемой всем заводом электроэнергии.
Обслуживание насосов
Обслуживание и контроль работы насосов выполняет персонал завода. Мониторинг работы оборудования осуществляется с помощью установленных на нем контрольно-измерительных приборов (КИП). Современный насос оснащен термопарами, которые измеряют температуру подшипников, самого насосного агрегата и электродвигателя. В случае, если насос перекачивает взрывопожароопасные вещества, он оснащен системой двойных торцевых уплотнений, и на бачке торцевого уплотнения тоже есть контрольные приборы: датчики давления, температуры, уровня. Помимо КИП состояние НКО контролируется системой блокировок: если один из параметров работы заходит в критическое значение, насос останавливается – однако в этом случае дефект уже успевает развиться.
Диагностикой оборудования занимается подразделение предприятия, но ремонт осуществляет обычно подрядчик, выигравший тендер на конкретные виды работ. При этом механическую часть насосного агрегата обслуживает и ремонтирует один подрядчик, ТОиР электродвигателя выполняет уже другая подрядная организация, а поверкой, проверкой и обслуживанием КИП занимается третья компания. Такая организация ТОиР создает сложности для контроля качества проведенных работ.
Все больше российских НПЗ для решения задач технического обслуживания и контроля работы насосов внедряют системы предиктивной аналитики. Такие системы уже внедрены, например, на Московском НПЗ, Омском НПЗ и Пермском НПЗ. Предиктивная аналитика позволяет им в режиме реального времени определять текущее техническое состояние насосов, выявлять зарождающиеся дефекты и не доводить до критического режима работы, аварийной остановки или поломки.
Система предиктивной аналитики обрабатывает данные, поступающие с датчиков, установленных на оборудовании, и с помощью математического моделирования может выявлять аномалии в его работе, прогнозировать его техническое состояние и заблаговременно сигнализировать о развивающихся дефектах. Она может подсказать оперативному эксплуатационному персоналу на что обратить внимание еще до того, как агрегат перейдет в критический режим работы и будут необратимы катастрофические изменения и последствия, связанные с выводом позиции в ремонт, поиском запчастей и длительными ремонтно-восстановительными работами. Кроме того, предиктивная аналитика помогает оценить выполнение и качество проведенных работ после очередного или внепланового ТОиР.
По оценке экспертов Ctrl2GO Solutions, помимо оптимизации процессов ТОиР, внедрение позволяет минимизировать отказы, простои и упущенную выгоду, сократить расход материально-технических ресурсов до 40% и продлить срок службы оборудования на 50%.
Расчет эффекта от внедрения предиктивной аналитики
Зарубежные проекты по внедрению решений прогнозной аналитики на нефтеперерабатывающих предприятиях позволили добиться впечатляющих результатов: повысить эффективность технического обслуживания динамического оборудования на 20-30 %, сократить внеплановые простои на 15-20 %, уменьшить объемы обслуживания и ремонта на 15-20 % и снизить энергопотребление на одну тонну нефти на 2-5 %.
Опыт западных стран показывает, что экономический эффект от таких систем тоже может быть значительным. Так, раннее выявление проблем помогло избежать значительных затрат:
- более $4 млн издержек при раннем обнаружении повреждений вращающегося оборудования (турбин, насосов и т. п.);
- $370 тыс. сэкономлено при раннем предупреждении проблем с перепускным клапаном теплообменника;
- более $500 тыс. сэкономлено при раннем обнаружении приближающегося отказа муфты заводского двигателя;
- $250 тыс. экономии в год при выявлении неэффективности насоса;
- $250 тыс. затрат избежали при раннем предупреждении о проблеме перепада давления в уплотнении подшипника;
- более $243 тыс. затрат избежали при раннем обнаружении неправильного позиционирования управляющего клапана.
Экономические итоги отечественных проектов пока подводить рано, однако в российских СМИ встречаются оценки ожидаемого экономического эффекта от внедрения системы предиктивной аналитики за счет снижения затрат на техническое обслуживание насосов и предотвращения незапланированного простоя оборудования.
Изменение годовой стоимости технического обслуживания насосного оборудования после внедрения системы предиктивной аналитики
До внедрения годовой бюджет на техническое обслуживание насосного оборудования на НПЗ производительностью 10 млн тонн нефти в год составлял около 900 млн рублей*. Общие годовые затраты на техническое обслуживание технологических насосов НПЗ – 7%. Снижение средней стоимости ремонта без непредвиденных отказов насосов – 30%. Таким образом, снижение годовых затрат на техническое обслуживание составит 900 000 000х0,07х0,3= 18 900 000 руб. (или 1,57 млн руб. в месяц). Таким образом, внедрение систем предиктивной аналитики для мониторинга и прогноза состояния насосного оборудования может существенно отразиться на затратах на ТОиР и представляется целесообразным для российских нефтеперерабатывающих и нефтехимических предприятий вне зависимости от специфики производства и эксплуатируемого НКО.
* годовой бюджет на ТО насосного оборудования определен на основе данных открытых закупок ведущих российских нефтяных компаний (Роснефть, Газпромнефть и др.)
ctrl2go.solutions
Статья опубликована в журнале «СФЕРА. Нефть и Газ» №3/2023
Статья в формате pdf →